Understanding the optimal service intervals for tractor components is a foundational aspect of agricultural machinery maintenance, playing a pivotal role in sustaining operational efficiency and prolonging machinery longevity. Defined as the predetermined times at which specific maintenance tasks should be performed on various tractor parts, these intervals serve as crucial benchmarks for upkeep.
Adhering rigorously to recommended service timelines not only ensures consistent performance but also mitigates the risk of unexpected breakdowns, ultimately minimizing downtime and maximizing productivity within farming operations.
Deviation from prescribed service intervals can lead to detrimental consequences, potentially resulting in decreased equipment reliability and compromised functionality. By meticulously following manufacturer guidelines on servicing frequencies for key components, farmers, agricultural equipment operators, and machinery maintenance technicians can proactively uphold the optimal condition of their tractors.
Embracing this preventive approach fosters a culture of precision in maintenance practices, safeguarding against costly repairs and preserving peak performance levels during critical farming seasons.
Through a comprehensive exploration of service schedules for essential tractor elements, this article aims to illuminate the intricacies surrounding efficient maintenance routines and equip stakeholders with indispensable insights for cultivating robust agricultural operations.
Engine Components.
In the realm of tractor maintenance, engine components hold a paramount position due to their role in power generation. Ensuring optimal performance and longevity of a tractor’s engine necessitates regular inspection of key elements such as engine oil, filters, and belts.
Engine oil serves as the lifeblood of the engine, providing lubrication while carrying away contaminants. Filters are essential in trapping harmful particles that could compromise engine efficiency, while belts facilitate the transmission of power within the engine system.
A widely accepted service interval for changing engine oil stands at approximately every 100 hours of operation. This proactive measure aims to prevent the buildup of damaging substances within the engine that could impede its functionality over time.
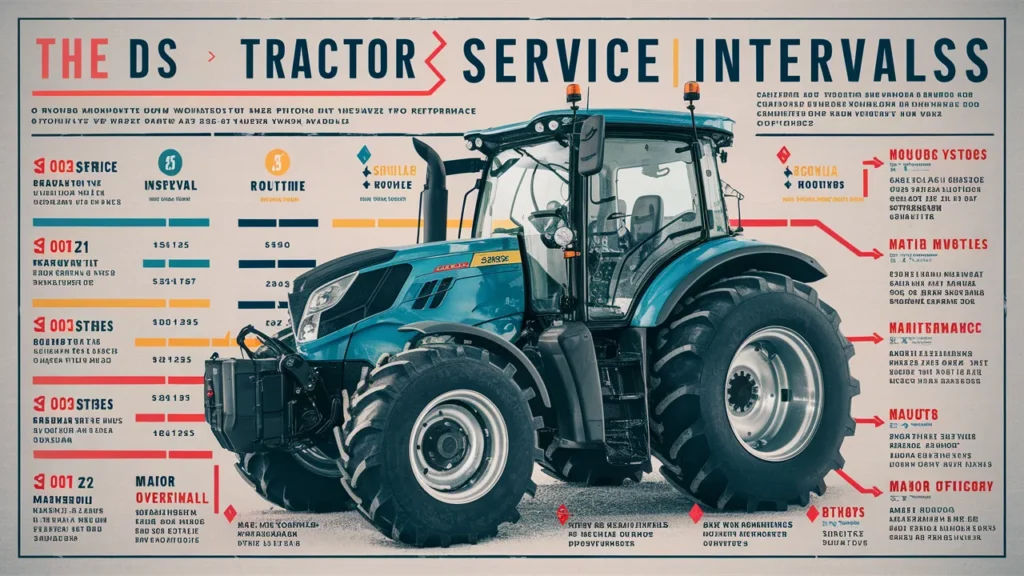
By sticking to this recommended interval diligently, operators can significantly reduce the risk of unexpected breakdowns and extend the lifespan of their tractor’s engine. Timely servicing not only safeguards against costly repairs but also ensures that the engine operates at peak efficiency, maximizing productivity on the farm.
Farmers and machinery maintenance technicians alike must prioritize adhering to these service intervals for engine components to uphold operational excellence throughout their equipment’s lifespan.
By recognizing the critical nature of these components and embracing routine inspections and maintenance practices, tractor owners can effectively mitigate potential issues that may arise from neglect or oversight. In essence, consistent care for engine components translates into sustained performance capabilities and enhanced reliability in agricultural operations.
Transmission and Gearbox.
Transmission and gearbox maintenance are critical aspects of ensuring the smooth operation and longevity of tractors. The service intervals for transmission fluid change can vary based on the specific tractor model and manufacturer recommendations.
Regularly changing the transmission fluid at prescribed intervals is essential to prevent wear and tear on internal components, maintaining optimal performance. For example, a popular tractor model may suggest changing transmission fluid every 300 hours to maintain proper lubrication and cooling for the transmission system.
In addition to periodic fluid changes, guidelines should be followed for checking transmission fluid levels at specified time intervals or when indicated by the manufacturer.
Monitoring transmission fluid levels ensures that the gearbox operates within the recommended parameters, reducing the risk of overheating or damage due to insufficient lubrication. A simple dipstick test or visual inspection can often reveal if additional transmission fluid is needed, allowing operators to address any issues promptly.
Proper maintenance of gears and clutch mechanisms further contributes to extending the lifespan of a tractor’s transmission system. Regular inspections for wear, proper alignment, and adjustments as necessary are crucial in preventing premature failures that could result in costly repairs or downtime.
Lubricating gears with high-quality oil according to manufacturer recommendations is key to reducing friction and heat generation within the gearbox, promoting smoother gear shifting operations over time. By adhering to service schedules and performing routine checks as outlined, operators can preserve the integrity of their tractor’s transmission system for years of reliable use.
Cooling System.
The cooling system in a tractor serves a vital function by regulating the temperature of the engine to ensure optimal performance and longevity. Typically, tractors employ a liquid-cooling system consisting of a radiator, water pump, coolant fluid, and thermostat.
This system functions by circulating coolant through the engine to absorb excess heat before returning it to the radiator for dissipation. Regular maintenance of the cooling system is imperative to prevent overheating, which can lead to engine damage and reduced efficiency.
Experts recommend flushing the radiator and changing the coolant at specific intervals to maintain the cooling system’s efficiency. The ideal frequency for this maintenance task can vary based on factors such as tractor usage, operating conditions, and manufacturer recommendations.
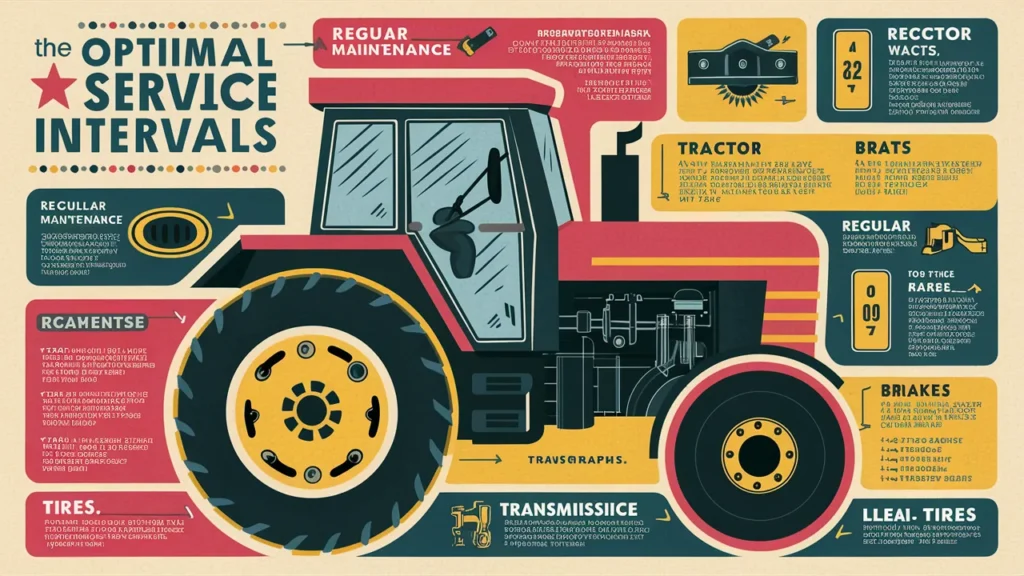
Generally, conducting a thorough flush and replacing the coolant every 2 years or after a certain number of operational hours ensures that debris and contaminants are removed from the system, allowing for optimal heat transfer and corrosion protection.
A well-maintained cooling system plays a crucial role in preventing overheating issues that can compromise tractor operation. For example, overlooking radiator flushing may result in sediment buildup that obstructs heat dissipation fins, leading to inefficient cooling.
In extreme cases, inadequate cooling can cause engine components to overheat, increasing wear and potentially causing costly malfunctions. By adhering to recommended service intervals for flushing the radiator and changing coolant, operators can safeguard their tractors against overheating-related problems while promoting consistent performance under varying workloads.
Hydraulic System.
Tractors rely on hydraulic systems to efficiently power various components like loaders, implements, and steering mechanisms. These systems utilize hydraulic fluids to transmit force and control functions through hoses and valves.
Regular inspection of these vital components is paramount in ensuring the tractor operates optimally. It is recommended to have hydraulic fluids and hoses inspected for wear and leaks at every 250 hours of operation or as specified by the manufacturer to prevent costly repairs caused by potential failures.
Maintaining proper hydraulic pressure levels within the system is essential for smooth operations. Regular checks during service intervals ensure that the correct pressure is maintained for efficient equipment functionality. Inadequate pressure can lead to sluggish performance or even failure of critical attachments.
By adhering to recommended service intervals, operators can detect any anomalies in hydraulic pressure early on, preventing any severe damage that could result from prolonged use with insufficient pressure levels.
An example illustrating the importance of maintaining the hydraulic system involves a scenario where a tractor loader fails to lift heavy loads as swiftly as usual due to a decrease in hydraulic pressure. If such symptoms are ignored or overlooked without adhering to service intervals, it could lead to a complete breakdown of the lifting mechanism, resulting in downtime during crucial farming operations.
Therefore, servicing at specified intervals not only ensures ongoing productivity but also extends the lifespan of the tractor’s hydraulics, ultimately reducing repair costs and avoiding operational setbacks.
Electrical Components.
Tractors rely on a plethora of electrical components to ensure smooth operations in the field. Essential elements include batteries, alternators, wiring connections, switches, lights, and fuses. The battery serves as the tractor’s power source, storing energy to start the engine and operate various electrical systems.
Alternators play a crucial role in recharging the battery while the engine runs. Wiring connections establish the pathways for electricity flow throughout the tractor, connecting different parts and systems to support functionality.
To maintain optimal performance and prevent unexpected failures, it is imperative to conduct periodic tests on these electrical components. Regular testing of batteries helps gauge their charge levels and health to avoid starting issues at critical times.
Similarly, assessing alternators ensures they are generating sufficient power to charge the battery effectively during operation. Checking wiring connections for any signs of wear or corrosion is essential to prevent short circuits or electrical malfunctions that could disrupt tractor functions.
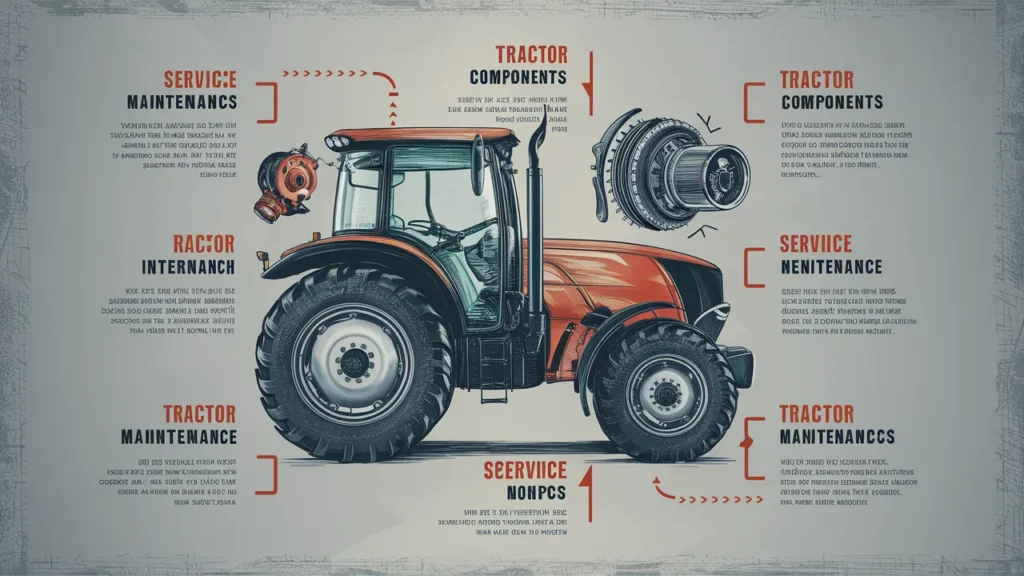
Ensuring reliable electrical functions within a tractor is paramount for both safety and productivity on the farm. Faulty electrical systems can lead to sudden breakdowns in critical moments or compromise overall efficiency in executing tasks.
Additionally, proper functioning lights contribute significantly to nighttime visibility and operator safety during low-light conditions. By adhering strictly to recommended service intervals for inspecting and maintaining these electrical components, operators can safeguard against costly downtime due to preventable electrical failures while maximizing operational effectiveness in challenging environments.
Regular inspection and testing of electrical components facilitate identifying potential issues early on before they escalate into major problems that require extensive repairs or replacements—proactive maintenance not only enhances reliability but also prolongs the lifespan of these critical tractor systems for sustained performance over time.
Chassis and Undercarriage.
The chassis of a tractor forms its structural backbone, providing support for various components and ensuring stability during operation. Beneath the tractor, the undercarriage encompasses parts like axles, suspension systems, and wheels that are crucial for mobility.
Regular maintenance of the chassis involves inspecting for signs of wear and tear, checking for corrosion, and addressing any potential issues related to alignment or stress points. Lubricating chassis parts such as steering mechanisms and pivot points is essential to reduce friction and prevent premature component failure.
Service recommendations for the chassis entail following manufacturer guidelines on lubrication schedules and periodic inspections. Depending on usage levels, lubricating grease fittings every 50-100 hours of operation can uphold proper functioning of moving parts in the chassis.
Similarly, conducting detailed examinations of undercarriage components like wheel hubs, bearings, or U-joints at designated intervals ensures early detection of any abnormalities that could escalate into larger problems if left unattended.
Neglecting maintenance tasks related to the chassis and undercarriage can have severe repercussions on overall tractor performance. Failure to lubricate essential parts adequately can result in increased wear and tear on components, eventually leading to system failures that may halt operations unexpectedly.
Ignoring signs of damage in the undercarriage could compromise safety during tractor use or result in costly repairs due to catastrophic breakdowns. Therefore, adhering strictly to service intervals for chassis maintenance is paramount in maximizing the lifespan and efficiency of agricultural equipment.
Conclusion.
In conclusion, adhering to the recommended service intervals for tractor components is paramount in ensuring the functionality, longevity, and safety of agricultural machinery.
By implementing a systematic approach to maintenance routines that encompass engine components, transmission and gearbox systems, cooling mechanisms, hydraulic functions, electrical elements, and chassis structures, operators can mitigate unexpected breakdowns and optimize performance efficiency.
The precision and consistency in servicing intervals not only serve as preventive measures against potential malfunctions but also contribute to overall operational reliability on the field.
It is imperative for farmers, agricultural equipment operators, and machinery maintenance technicians to recognize that neglecting routine service intervals could compromise the integrity of tractor components over time.
With a firm grasp on the service recommendations provided for various aspects of tractor maintenance outlined in this article, individuals can proactively uphold the operational standards of their equipment while enhancing productivity levels within agricultural settings.
Embracing a disciplined approach to servicing intervals ultimately fosters a culture of diligence and precision in managing tractor components for sustainable performance outcomes in farm operations.